Fire and Safety in the EV Industry
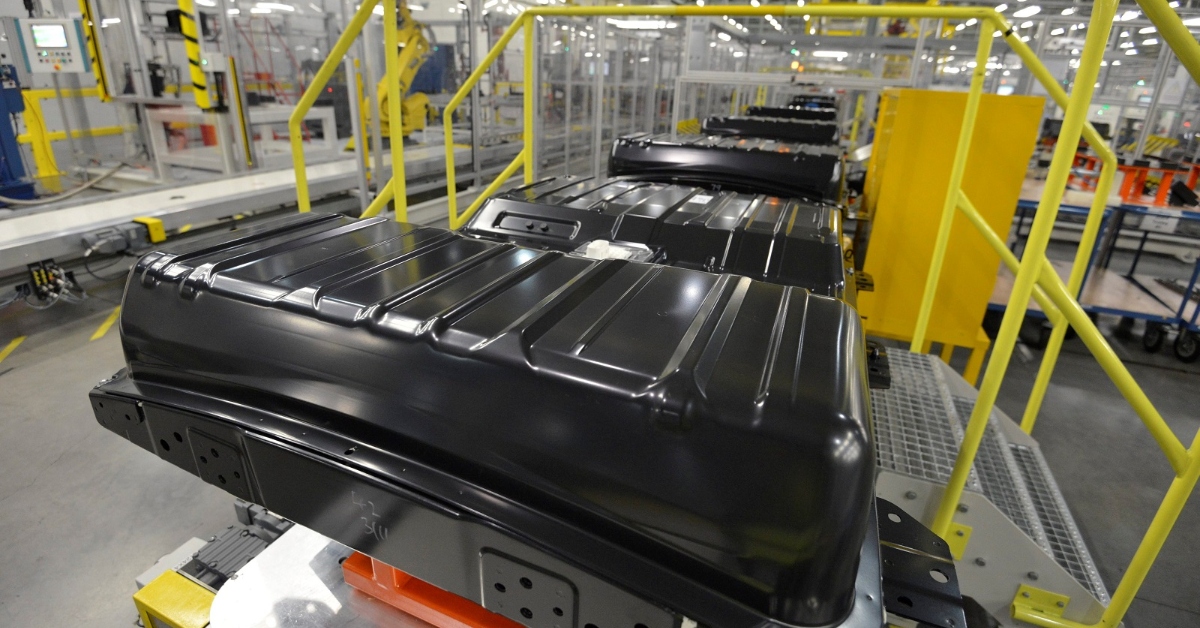
Solutions for the upcoming Electrical Vehicle industry using temperature monitoring
INTRODUCTION
The electric vehicle or EV industry has been growing exponentially over the last few years. It has gained popularity due to the alarming crisis of climate change and an urgent need to find an alternative to current fuel-powered vehicles.
Since the demand for electric vehicles has escalated significantly so has the production and manufacturing of battery packs and the challenges associated with it. This surge in the production of electric vehicles has also brought forward multiple headlines of fire incidents. These incidents are not localized to small businesses but also include companies like Tata, TESLA, and OLA. This topic is very fast and there might be multiple reasons behind all the incidents.
One of the high-tech solutions that can help to reduce a few incidents is thermal imaging.
This application note covers predictive maintenance and material research of electric vehicles.
APPLICATIONS OF THERMAL IMAGING EV INDUSTRY
WELDING
Lithium cell units need to be welded together to form a battery back. However, if the welding is not done properly, faults may arise in the final product. The resistance and output may be affected, and the longevity of the battery is directly affected. Usually, welding is checked manually by the factory workers which is a destructive method of testing, with which the cell may be ruptured.
A non-destructive and non-contact method to check the welded joint is by using thermal imaging. We can easily detect a poorly welded joint due to the slightly different temperature displayed by its seam. An uneven seam or a slightly raised temperature indicates faulty welding.
This method of testing already prevails across industries in the United States.
CELL LEAKAGE
Almost invisible to the naked eye, cell leakage can occur at any time during the manufacturing process and can damage the battery pack. A cell that is leaking can be extremely dangerous if it comes in contact with the skin. We can use methods like the mass spectrometer to detect leakage but there is a better method to detect these small leakages: thermal imaging.
When the seal of the cell is ruptured, the liquid is deposited on the outer layer of the cell and a temperature difference is detected. A high-resolution thermal camera can efficiently identify these minute leakages within a matter of seconds without contact as shown in the figure.
Cell leak identification using T-Series camera
UNEVEN HEATING
Although with thorough testing at every stage, sometimes a faulty cell might still enter the production line. During the testing phase, faulty cells may display a slight temperature difference. This may be invisible to the human eye but can be easily captured using a thermal camera.
As seen in the below Figure, the slightly elevated temperature is captured by the camera with a temperature reading accurate to the decimal.
Uneven heating displayed by the lithium battery unit
Another example of uneven heating during manufacturing is during testing of the battery packs after assembling them. During the charge and discharge cycles, battery packs tend to heat up. However, during this testing phase, there is a high risk of the battery pack catching fire if the temperature is not monitored. This can be done using a thermocouple, a non-destructive contact method but it is only possible to monitor the temperature of one point at a time. If a lithium battery back catches fire in the facility, it will be difficult to put out as lithium reacts really fast and the fire is difficult to put out because lithium reacts with water when in contact.
CHARGING AND DISCHARGING
The last phase of testing includes charging and discharging the lithium-ion battery. During this phase, the temperature of the battery pack may rise to 5 or 6 degrees Celsius above the ambient temperature. Using a thermal imager, we can record the surface temperature of the lithium-ion battery pack and estimate the internal temperature without touching it.
We can clearly see the hotspots in the battery pack through the surface while it is being charged. This helps us isolate a potential issue and the location of the issue.
Batteries being tested can be monitored around the clock to prevent potential fires if any unit heats up.
EV VEHICLE
The EV vehicle comprises 3 main components, the battery, motor, and invertor. Once the vehicle is assembled, thermal technology can be used to monitor its temperature behavior while it's being used.
This application is extremely valuable considering the recent rise of EV fires in India as it doesn’t only provide solutions for battery manufacturing but also is capable of monitoring other components of the machine.
An image of the interior of an EV
CONCLUSION
Although there are multiple preventative methods that can be used in the line of production of electrical vehicles, this solution provides predictive maintenance, fire, and safety for this industry. Thermal imaging can be applied at various steps during the manufacturing process to monitor the target object and check for defaults.
As the demand and supply both increase in this industry, so will the need to have more reliable testing and data for prevention and safety, in which thermal imaging proves to be a more than viable option to reduce the probability of an electrical vehicle failing.
FLIR Total Solutions for the EV Battery Industry
FLIR Thermal Studio Suite Analysis and Reporting Software
Professional Reports that Help Your Customer and Your Business
The right image analysis and reporting software can greatly improve your business by making it easier for you and your customers to understand the problem and feel confident that you fixed it.
The advanced analysis and decision-making support offered in FLIR Thermal Studio Pro includes a rich set of measurement tools, batch processing, the ability to pre-plan inspection routes, and customized report templates.
Product Offerings for the EV Battery Industry